Water efficiency in sugar and confectionery manufacturing is a critical aspect of sustainable industrial practices. As the industry faces increasing environmental concerns and regulatory pressures, optimizing water use and managing wastewater effectively have become essential. This blog delves into the various facets of managing wastewater water efficiency and the innovative strategies being adopted to achieve sustainability in sugar and confectionery manufacturing.
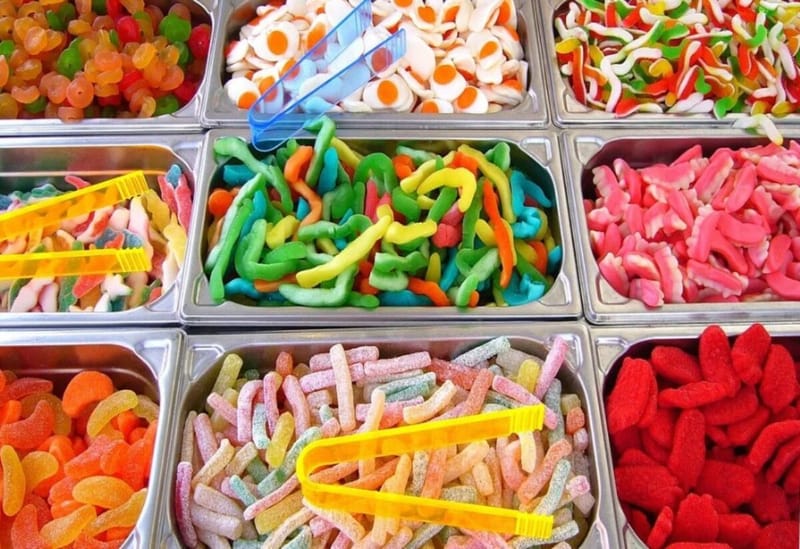
The Importance of Water Conservation in Sugar and Confectionery Production
Water is used extensively in the manufacturing processes of sugar and confectionery goods, including washing, boiling, cooling, and a variety of other procedures. However, the high water use and possibility for large amounts of wastewater raise considerable environmental issues. Improving water efficiency not only helps to preserve this vital resource, but it also reduces operational costs, increases regulatory compliance, and contributes to the accomplishment of business sustainability goals. Manufacturing facilities can reduce their environmental effect by optimizing water use, ensuring that water is available for future use. Furthermore, businesses that prioritize water conservation frequently distinguish themselves by demonstrating their commitment to environmental care and corporate accountability.
Implementing water reuse and recycling technologies improves water efficiency. Recycling water from operations such as rinsing during the preliminary washing phases decreases the requirement for fresh water. This saves water and reduces wastewater volume, easing the pressure on treatment facilities. Closed-loop systems maximize resource efficiency and reduce waste, resulting in a more sustainable production cycle. Investing in water recycling systems leads to long-term cost savings and operational efficiencies.
Condensate Recovery: Steam plays a crucial role in sugar processing for heating and boiling. Recovering steam condensate for reuse as boiler feedwater reduces fresh water requirements and energy consumption. Condensate recovery systems capture and recycle condensate from steam processes, reducing the need for fresh makeup water. This practice conserves water and enhances energy efficiency by retaining heat in the recovered condensate. Implementing condensate recovery systems demonstrates a proactive approach to resource management and sustainability.
Water Monitoring and Management
Water Audits: Detailed water audits identify high-consumption areas and potential savings by mapping water usage across production stages. This enables targeted interventions to reduce waste and optimize consumption, fostering a culture of water stewardship. Regular audits ensure continuous improvement and adaptation to operational needs.
Leak Detection and Repair: Continuous monitoring systems detect leaks early, preventing water wastage. Implementing advanced leak detection technologies, such as sensors and automated monitoring systems, helps in quickly pinpointing leaks for prompt repair. Proactive maintenance programs are crucial for maintaining the integrity of the water system and ensuring optimal efficiency.
Automated Controls: Sensors and automated controls regulate water flow and pressure, ensuring optimal usage. Real-time monitoring and control systems adjust water use based on process requirements, preventing overuse. These systems provide valuable data on consumption patterns, aiding in targeted conservation measures and overall efficiency improvement. Integration of smart technologies enhances water management capabilities, reducing waste and improving efficiency.
Wastewater Treatment and Management
Effective wastewater management is critical due to the high volume of water used and the potential for significant pollution loads. Implementing robust wastewater treatment systems ensures that water discharged from the facility meets environmental standards and can potentially be reused within the manufacturing process.
Wastewater Characteristics: Sugar manufacturing wastewater typically contains high levels of organic matter, including sugars, which lead to high biological oxygen demand (BOD) and chemical oxygen demand (COD). It also contains solids and suspended particles like pulp and fibers. Understanding the composition of wastewater is essential for designing effective treatment systems. Regular monitoring and analysis of wastewater quality help in identifying contaminants and tailoring treatment processes to address specific pollution loads.
Pre-Treatment: Screens remove large solids and debris, while sedimentation tanks allow solids to settle, reducing the load on subsequent treatment processes. This stage prepares wastewater for advanced treatment by eliminating easily separable contaminants, enhancing performance, and lowering costs and maintenance needs.
Primary Treatment: Chemicals for coagulation and flocculation aggregate fine particles into larger flocs, which are removed by sedimentation or flotation. This step reduces pollutant load, improves efficiency of further treatment stages, and helps meet environmental regulations.
Secondary Treatment: Aerobic biological methods like activated sludge processes or biofilm reactors degrade organic matter, while anaerobic digestion treats high-strength organic wastewater, producing biogas and reducing sludge volume. These methods significantly lower BOD and COD levels by leveraging microorganisms.
Tertiary Treatment: Advanced filtration methods, such as sand filters and membrane bioreactors, remove remaining solids and pathogens, while nutrient removal processes eliminate excess nitrogen and phosphorus. This stage achieves high purification levels, making treated water suitable for reuse.
Disinfection: Chlorination, UV, or ozone treatment disinfects treated wastewater before discharge or reuse. These processes eliminate pathogens and ensure water safety, supporting sustainable reuse. Different methods are employed based on the intended use of the treated water.
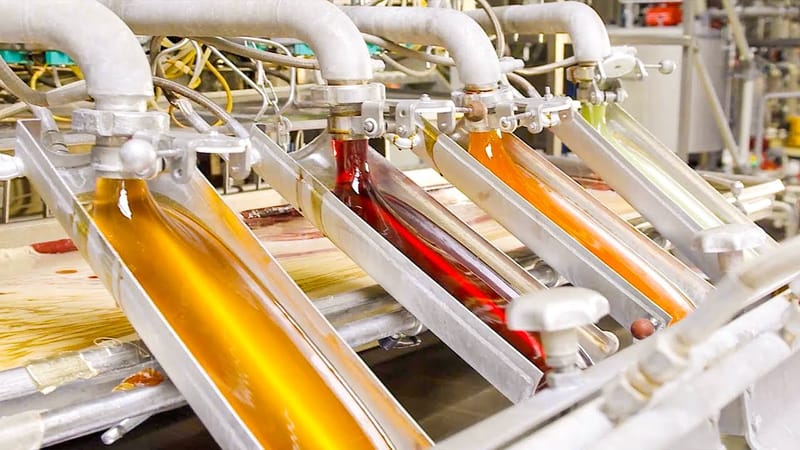
Reuse and Recycling of Wastewater
Treated wastewater can be reused in non-potable applications such as cooling towers, boiler feedwater, and irrigation systems. This minimizes the need for fresh water and decreases wastewater discharge volumes. Reusing treated wastewater allows enterprises to dramatically reduce their environmental footprint while also promoting a circular economy strategy. Implementing effective reuse systems involves careful planning and effort, but it provides long-term benefits in terms of sustainability and cost savings.
Zero Liquid Discharge (ZLD): Implementing advanced treatment processes to achieve ZLD means that all wastewater is treated and reused within the facility, eliminating discharge and minimizing environmental impact. ZLD systems involve the use of multiple treatment stages to recover and recycle water, leaving minimal or no liquid waste. Adopting ZLD practices demonstrates a strong commitment to environmental stewardship and aligns with the highest standards of sustainability.
Innovation and Technology
Water-Saving Technologies: Investing in high-efficiency nozzles for cleaning, waterless cooling systems, and advanced metering infrastructure can lead to significant water savings. Modern technologies offer various solutions to reduce water consumption without compromising on productivity or quality. Continuous research and development in water-saving technologies provide new opportunities for improving efficiency and sustainability in manufacturing processes.
Smart Water Management Systems: Integrating IoT and data analytics to monitor water usage patterns, predict water needs, and optimize water distribution across the facility ensures efficient water use and identifies areas for further improvement. Smart water management systems enable real-time monitoring and control, providing valuable insights into water consumption patterns and helping manufacturers make informed decisions. By leveraging data and technology, companies can enhance their water management capabilities and achieve significant improvements in efficiency and sustainability.
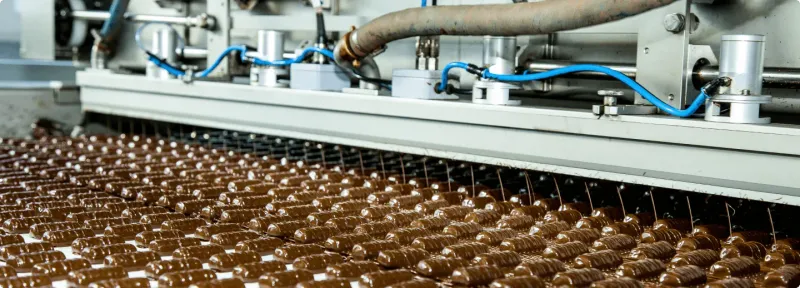
Environmental and Economic Benefits
Reduced Freshwater Consumption: Efficient water use and recycling reduce the need for fresh water, conserving local water resources. By optimizing water use, manufacturers can lessen their impact on local water supplies, ensuring that sufficient resources are available for other uses, such as agriculture and community needs. Reducing freshwater consumption also aligns with global efforts to address water scarcity and protect vital ecosystems.
Lower Operating Costs: Reduced water and wastewater treatment costs through efficient practices and technologies can lead to significant savings. By implementing water-efficient practices, manufacturers can lower their operational expenses related to water procurement, treatment, and disposal. These cost savings can be reinvested in further sustainability initiatives, driving continuous improvement and innovation.
Regulatory Compliance: Meeting or surpassing environmental regulations and wastewater discharge criteria is critical for avoiding fines and projecting a positive public image. Compliance with regulatory regulations displays a company's commitment to environmental responsibility and fosters trust among stakeholders, such as consumers, investors, and regulatory agencies. Proactively addressing water efficiency and wastewater management ensures that businesses are prepared to fulfill current and future regulatory requirements.
Sustainability: Improving the overall sustainability of the manufacturing process lowers the company's environmental footprint and promotes a positive public image. Sustainable water management methods contribute to larger corporate social are well-prepared to meet current and future regulatory challenges. Prioritising sustainability allows enterprises to attract environmentally conscientious customers and investors, improving their market position and long-term viability.
Conclusion
Implementing comprehensive water efficiency and wastewater management techniques in sugar and confectionery manufacturing is not only an environmental requirement, but also a good commercial practice. Manufacturers may save considerable amounts of water, lower operational costs, and reduce their environmental effect by optimizing processes, implementing modern treatment technology, and cultivating a sustainable culture. As the sector strives for greater sustainability, these practices will become increasingly important to maintaining long-term profitability and resilience. Water efficiency and sustainability are critical for the sugar and confectionery production sector's long-term growth and success.