Water is a vital resource in snack food manufacturing, integral to every aspect of the production process, from ingredient preparation to equipment cleaning. As environmental concerns and resource management become increasingly critical, snack food manufacturers are compelled to rethink and enhance their water usage strategies. The following explores innovative and advanced approaches to water efficiency, aiming to revolutionise how water is managed and conserved in this industry.
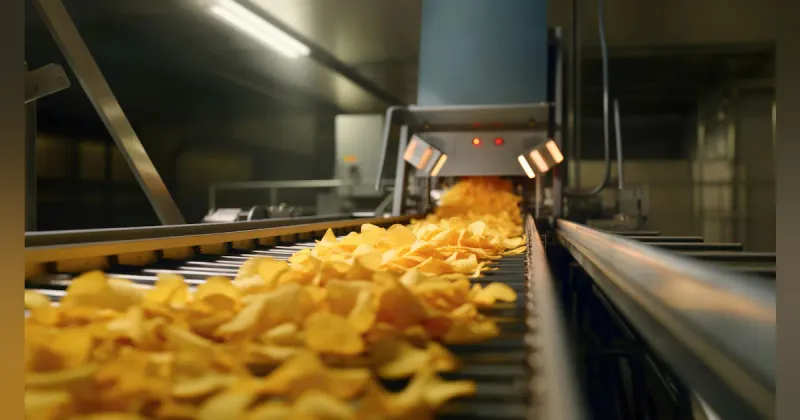
Cutting-Edge Water Recycling Technology
The application of cutting edge recycling technologies is one of the water efficiency strategies that has the greatest transformative power. At the forefront of this innovation are membrane filtration systems like nanofiltration and reverse osmosis. Process water can be recycled inside the production process thanks to the systems' ability to cleanse and purify it. Manufacturers may drastically lower their need on fresh water supplies by eliminating impurities and recovering high-quality water.
Additionally, closed-loop water systems are revolutionising water management. These systems continuously recirculate and purify water, creating a virtually closed cycle within the facility. By integrating advanced filtration and treatment technologies, closed-loop systems minimize the need for fresh water input and substantially reduce wastewater output. This approach not only conserves water but also enhances overall efficiency by optimizing the use of available resources.
Innovative Water Treatment Approaches
Incorporating advanced chemical treatments into wastewater management is another innovative strategy gaining traction. Techniques such as electrocoagulation and ion exchange offer sophisticated solutions for treating wastewater. Electrocoagulation uses electrical currents to destabilize and remove contaminants, while ion exchange involves exchanging ions between water and a resin to remove impurities. These methods effectively purify wastewater, making it suitable for reuse or discharge, and recovering valuable resources in the process.
Biological water treatment is also making waves in water efficiency. By utilizing microorganisms or bioreactors, manufacturers can biologically treat wastewater, breaking down organic contaminants efficiently. This process not only makes wastewater suitable for reuse but also alleviates the load on conventional treatment systems, contributing to overall resource efficiency.
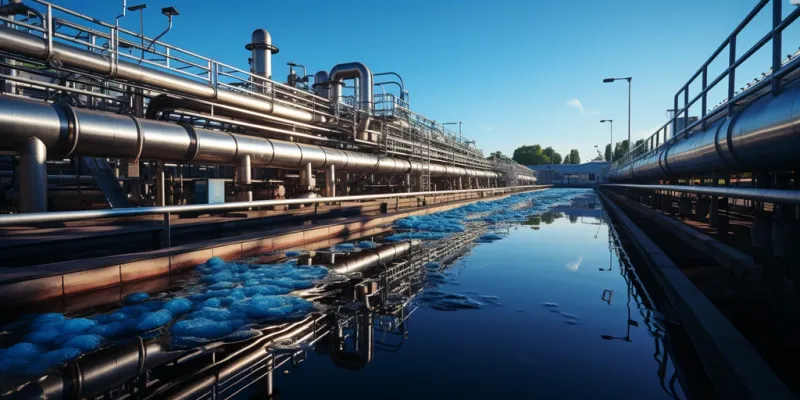
On-Site Water Desalination and Zero Liquid Discharge
On-site desalination is a practical option for establishments located in areas where there are brackish or salinized water sources. These difficult water sources can be converted into high-quality water that is appropriate for industrial operations via desalination technology. This promotes more general sustainability objectives and lessens reliance on outside freshwater supplies.
Reaching Zero Liquid Discharge (ZLD) is a further significant but ambitious approach. ZLD systems are made to recover and reuse water from industrial operations in order to completely eliminate wastewater outflow. These systems make use of a variety of treatment techniques, including as evaporation and sophisticated filtering, to guarantee that no liquid waste is discharged into the environment. Manufacturers may shut the water consumption loop and drastically lessen their environmental impact by adopting ZLD systems.
Smart Water Resources and Technology Pairing
The way manufacturers monitor and optimize water use is changing as a result of the incorporation of smart technologies into water management procedures. Real-time monitoring of water consumption is made possible by IoT devices and smart sensors, which can identify inefficiencies and provide useful information for optimization. Manufacturers may lower overall water consumption, improve operational efficiency, and make well-informed decisions with this data-driven strategy.
Optimizing water management is also greatly aided by artificial intelligence (AI). AI-powered software is able to forecast and optimize water use by analyzing previous data and current conditions. Manufacturers may optimize their water management plans, increasing the effectiveness of water treatment systems and lowering water use, by utilizing machine learning models.
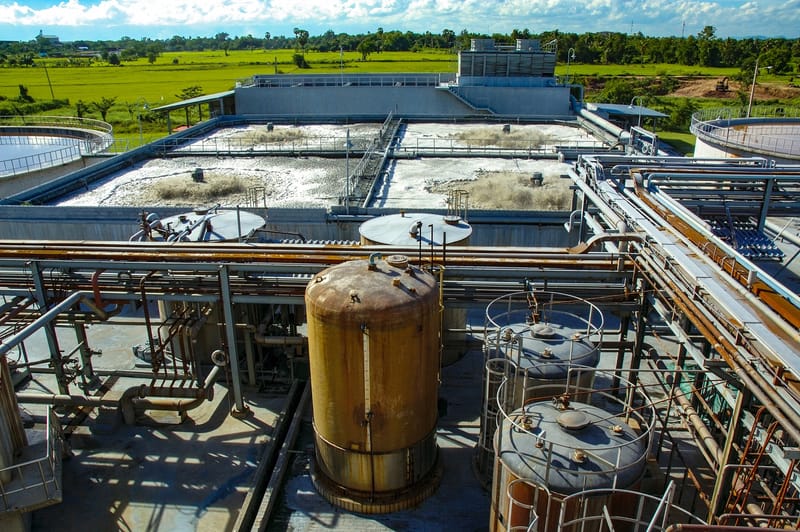
Water-Efficient Processing and Cleaning Technologies
Innovative processing techniques that minimize water use are contributing to significant efficiency gains. For instance, adopting dry methods for ingredient handling and preparation can substantially reduce the volume of water needed. These methods not only conserve water but also streamline production processes.
In the realm of cleaning technologies, advancements such as dry ice blasting and high-pressure air systems are reducing the need for water in cleaning operations. These methods enhance cleaning efficiency while minimizing water use, contributing to overall resource conservation.
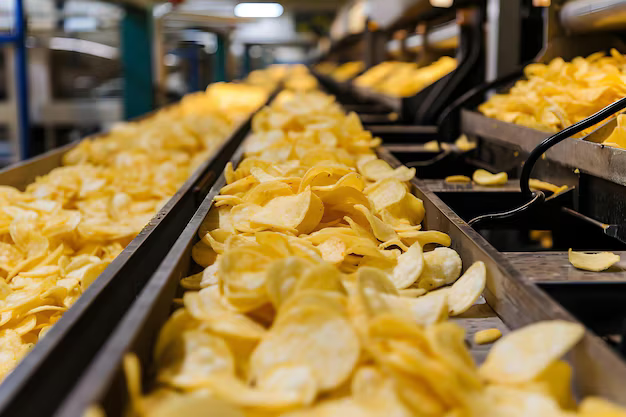
Dynamic Water Use Scheduling and Facility Design
Dynamic water use scheduling is another strategy that can lead to substantial water savings. By adjusting water use in real-time based on production schedules and demand, manufacturers can optimize water flow and reduce waste. This approach ensures that water resources are used efficiently, aligning consumption with production needs.
Incorporating water-efficient design principles in facility construction or renovation further enhances water conservation efforts. Designing facilities with water-saving fixtures, efficient cooling systems, and minimal irrigation requirements can contribute to overall water efficiency.
Collaboration and Innovation in Water Management
Collaboration with suppliers and partners who prioritize water efficiency can amplify water conservation efforts. By sourcing ingredients from suppliers who use innovative water-saving agricultural practices, such as hydroponics or vertical farming, manufacturers can reduce their water footprint.
Exploring biotechnological solutions, such as enzyme treatments, can also lead to water savings. These treatments can enhance processing efficiency or eliminate the need for water in certain operations, further supporting sustainability goals.
Employee Engagement and Education
Engaging employees in water conservation efforts is crucial for achieving sustainability goals. Implementing gamification strategies, such as challenges and leaderboards, can motivate employees to participate in water-saving initiatives. Additionally, regular training programs can educate staff about best practices for water conservation, fostering a culture of sustainability within the facility.
Evaluation of Water Risk and Prospects for the Future
Developing methods to limit potential consequences on manufacturing operations requires regular water risk assessments. Manufacturers are better able to anticipate problems and promote sustainable water management when they assess the quality and availability of nearby water sources.
Adopting cutting-edge water management techniques will be essential to forming a more sustainable future as the sector develops further. Snack food producers may set the standard for environmental stewardship and water efficiency by using cutting-edge technologies, streamlining operations, and encouraging a culture of conservation.
By adopting these comprehensive and innovative approaches, snack food manufacturers can not only enhance their water efficiency but also contribute to a more sustainable and resource-conscious industry.