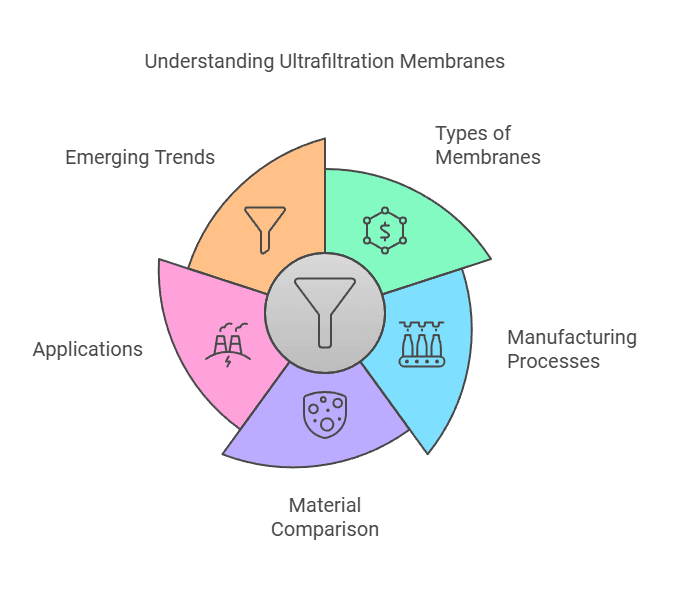
Property | PVDF (Polyvinylidene Fluoride) | PTFE (Polytetrafluoroethylene) |
Chemical Resistance | Good resistance to most acids, bases, and solvents | Excellent resistance to almost all chemicals |
Thermal Stability | Moderate (up to ~140°C) | Very high (up to ~260°C) |
Hydrophobicity | Naturally hydrophobic but modifiable to hydrophilic | Highly hydrophobic; surface treatment needed for hydrophilic use |
Mechanical Strength | Good tensile and impact strength | Exceptional tensile strength and durability |
Fouling Resistance | High, especially in hydrophilic forms | Very high, particularly for oil-based fouling |
Applications | Water treatment, wastewater, biopharma, food & beverage | Industrial wastewater, chemical processing, oil-water separation |
Cost | Lower compared to PTFE | Higher due to complex manufacturing processes |
Ultrafiltration (UF) membranes are at the forefront of modern filtration technologies, playing a pivotal role in industries ranging from water treatment to biotechnology. With a wide array of materials, manufacturing techniques, and applications, UF membranes are tailored to meet diverse needs. This blog delves deep into the types of UF membranes, their properties, manufacturing processes, and a detailed comparison of two key materials—PVDF (Polyvinylidene Fluoride) and PTFE (Polytetrafluoroethylene).
Types of UF Membranes
UF membranes are classified based on their materials and structures, which directly influence their performance and applications. The primary types include:
1. Polymeric UF Membranes
These are the most commonly used membranes due to their versatility, cost-effectiveness, and ease of fabrication. Key materials include:
- PVDF (Polyvinylidene Fluoride): Renowned for its chemical resistance, mechanical strength, and durability.
- PES (Polyethersulfone): Offers excellent thermal stability and hydrophilicity, making it ideal for biological and pharmaceutical applications.
- PS (Polysulfone): Similar to PES but with slightly less thermal stability, commonly used in wastewater treatment.
- PTFE (Polytetrafluoroethylene): Known for its unmatched chemical resistance and high thermal stability, suitable for extreme environments.
2. Ceramic UF Membranes
Manufactured from materials like alumina or zirconia, ceramic membranes are highly durable and resistant to extreme pH and temperature conditions. They are predominantly used in industrial processes requiring robust filtration solutions.
Hollow Fiber Membranes
These membranes are made from polymeric materials and are characterized by their high surface area-to-volume ratio. They’re commonly employed in water treatment and industrial separations.
Flat Sheet Membranes
Flat sheet membranes are often used in submerged systems and are typically made from polymeric materials like PVDF or PES. Their applications include municipal water treatment and membrane bioreactors (MBRs).
Tubular Membranes
These membranes have a tubular structure and are commonly used in treating high-suspended solids or oily wastewater. Materials such as PTFE are often employed for their durability in harsh conditions.
Manufacturing Processes: NIPS vs. TIPS
Two primary manufacturing techniques for UF membranes are Non-solvent Induced Phase Separation (NIPS) and Thermally Induced Phase Separation (TIPS).
1. NIPS (Non-solvent Induced Phase Separation)
- Process: A polymer solution is immersed in a non-solvent bath, inducing the polymer to precipitate and form a porous structure.
- Result: Produces asymmetric membranes with a dense skin layer for selectivity and a porous substructure for support.
- Applications: Widely used in water and wastewater treatment due to controlled pore size.
2. TIPS (Thermally Induced Phase Separation)
- Process: A polymer and solvent are mixed at high temperatures and cooled to induce phase separation.
- Result: Typically creates symmetric membranes with uniform porosity, offering consistent filtration performance.
- Applications: Suitable for industrial applications requiring high mechanical and chemical stability.
PVDF vs. PTFE: A Detailed Comparison
The choice of material significantly impacts the performance, durability, and cost of UF membranes. Here is a detailed comparison of PVDF and PTFE membranes:
Property | PVDF (Polyvinylidene Fluoride) | PTFE (Polytetrafluoroethylene) |
Chemical Resistance | Good resistance to most acids, bases, and solvents | Excellent resistance to almost all chemicals |
Thermal Stability | Moderate (up to ~140°C) | Very high (up to ~260°C) |
Hydrophobicity | Naturally hydrophobic but modifiable to hydrophilic | Highly hydrophobic; surface treatment needed for hydrophilic use |
Mechanical Strength | Good tensile and impact strength | Exceptional tensile strength and durability |
Fouling Resistance | High, especially in hydrophilic forms | Very high, particularly for oil-based fouling |
Applications | Water treatment, wastewater, biopharma, food & beverage | Industrial wastewater, chemical processing, oil-water separation |
Cost | Lower compared to PTFE | Higher due to complex manufacturing processes |
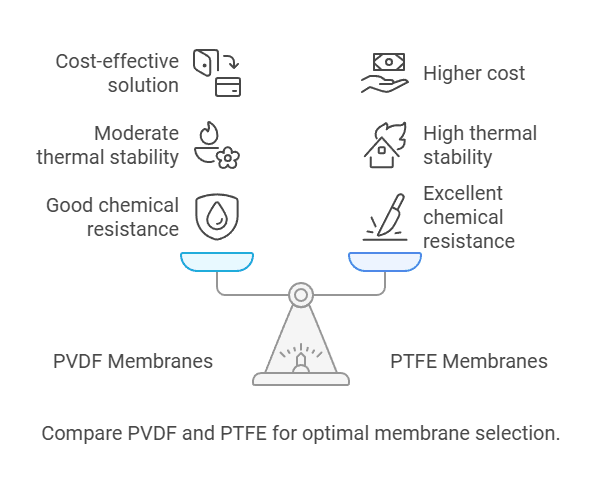
Key Takeaways:
- PVDF: An excellent choice for water and wastewater treatment applications where cost and performance need a balance.
- PTFE: Ideal for extreme environments with aggressive chemicals or high temperatures but comes at a higher cost
Manufacturers and Materials
The global UF membrane market features a diverse range of manufacturers, each specializing in specific materials and technologies. Below is an overview of some key players and the types of membranes they produce:
Manufacturer | Materials Used |
---|---|
Alfa Laval | PVDF, PES |
DOW | PVDF, PES |
DuPont (Inge) | PES, PVDF |
Toray | PVDF, PTFE |
Koch Membrane Systems | PES, PVDF |
Hyflux | PVDF |
NX Filtration | PES, Modified PES |
Pall Corporation | PES, PVDF |
Pentair | PVDF, PES |
PolyCera | Proprietary hybrid materials |
Microdyn-Nadir | PES, PVDF |
Nitto Denko (Hydranautics) | PVDF, PES |
Applications of UF Membranes
UF membranes are versatile and cater to a wide array of applications:
1. Water Treatment
UF membranes are pivotal in potable water production, removing suspended solids, bacteria, and viruses. Materials like PVDF are particularly favored for their durability and cost-effectiveness.
2. Wastewater Treatment
Industrial and municipal wastewater treatment relies heavily on UF membranes for their ability to handle high suspended solids and organic load. PTFE membranes are often chosen for their chemical resistance in harsh environments.
3. Biopharmaceuticals
In the biopharma sector, UF membranes are used for protein separation, virus removal, and cell harvesting. Hydrophilic PES membranes are common due to their biocompatibility.
4. Food and Beverage
Applications include milk protein concentration, juice clarification, and wine filtration. PES and PVDF membranes dominate this sector.
5. Industrial Processes
Membranes play a crucial role in oil-water separation, chemical recovery, and metal processing. PTFE membranes are preferred for their resilience in extreme conditions.
Emerging Trends and Innovations
- Material Advancements: Research into hybrid materials like those used by PolyCera is opening new avenues for improved performance and durability.
- Sustainability: Manufacturers are focusing on creating membranes with lower environmental impact, such as those with longer lifespans and reduced fouling rates.
- Automation and IoT Integration: Smart filtration systems equipped with sensors and IoT capabilities are enabling real-time monitoring and predictive maintenance.
Choosing the Right UF Membrane
Selecting the appropriate UF membrane requires careful consideration of several factors:
- Application Requirements: For potable water, PVDF is ideal, while PTFE suits extreme industrial settings.
- Operating Conditions: Assess temperature, chemical exposure, and fouling potential.
- Cost: Balance initial investment with long-term operational efficiency.
- Manufacturer Support: Opt for reliable suppliers with a track record in your industry.
Conclusion
UF membranes are indispensable in modern filtration systems, offering solutions for water purification, industrial separation, and beyond. Understanding the nuances of materials like PVDF and PTFE, their manufacturing processes, and their suitability for specific applications is key to optimizing performance and cost-efficiency. As the field evolves with new materials and technologies, UF membranes will continue to play a critical role in addressing global water and filtration challenges.