The global jam and jelly industry has evolved significantly, with growing consumer demand for natural, organic, and sustainably produced food products. As this sector expands, so does the need for responsible production methods, particularly in managing environmental impacts. One of the most critical yet overlooked aspects of food manufacturing is wastewater treatment. In jam and jelly production, wastewater can contain high levels of organic matter, sugars, fruit residues, and processing chemicals. Addressing these issues with sustainable practices is key to minimizing environmental damage and meeting regulatory standards.
This blog explores the unique challenges of wastewater management in jam and jelly processing and outlines sustainable practices and technologies to improve treatment and water use efficiency.
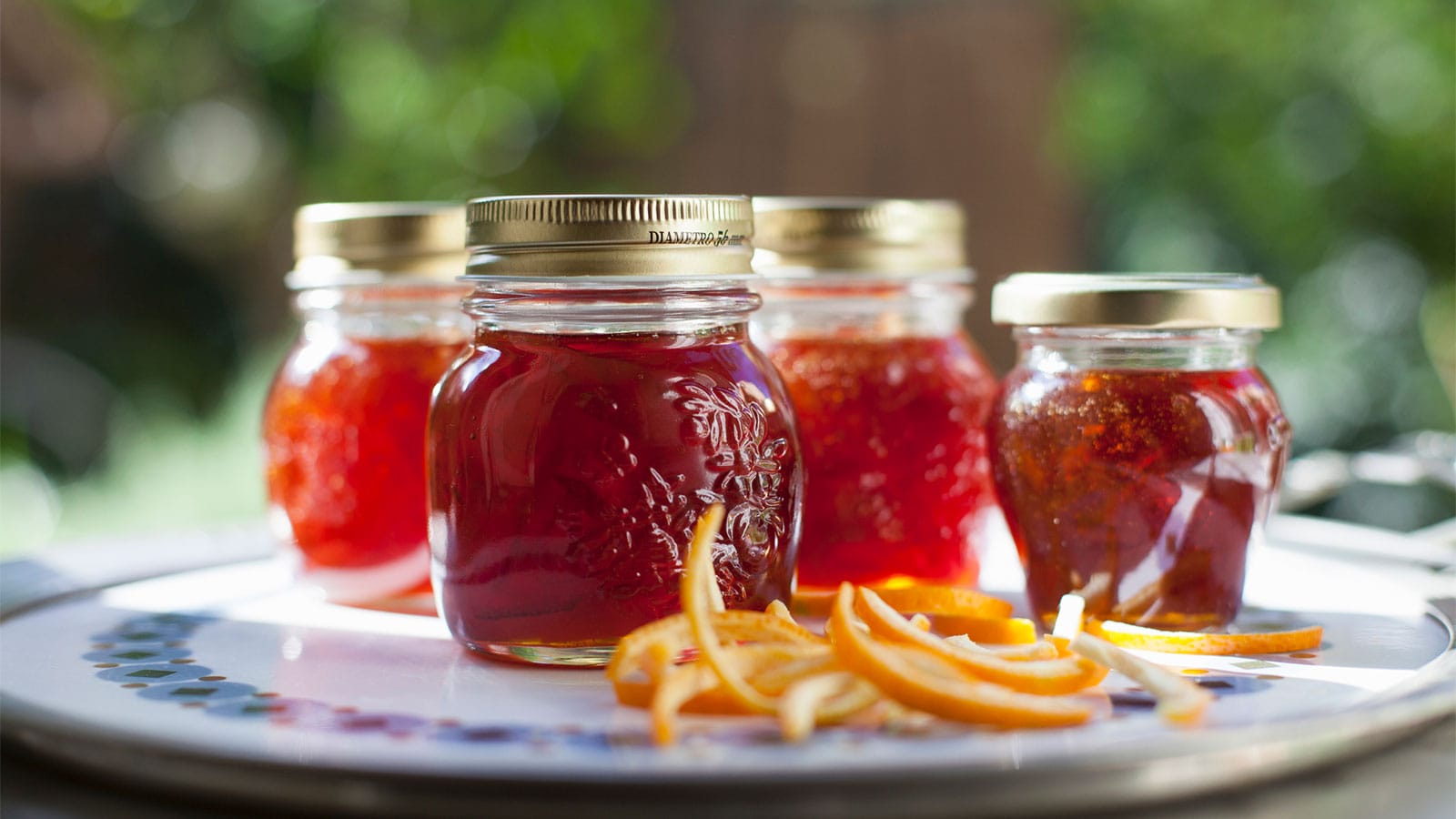
Wastewater Challenges in Jam and Jelly Production
The production of jams and jellies involves various stages, from fruit preparation to cooking, jarring, and packaging. Each step generates wastewater with distinct characteristics. Here are some of the common contaminants found in the wastewater of jam and jelly manufacturing plants:
Organic Matter
Fruits, the primary ingredients in jams and jellies, contribute large amounts of organic waste. This includes peels, pulp, seeds, and sugars. As these organic substances break down, they increase the Biological Oxygen Demand (BOD) and Chemical Oxygen Demand (COD) of wastewater. High BOD and COD levels can severely deplete oxygen levels in water bodies if discharged untreated, resulting in damage to aquatic ecosystems.
Sugars
During the jam-making process, substantial amounts of sugar are added to fruits, contributing to the high sugar content in wastewater. These sugars promote microbial growth, which can further elevate BOD and COD levels, making treatment more challenging.
Pectin and Additives
A gelling agent that is often used in jams and jellies is Pectin. Its presence in wastewater can increase viscosity, complicating the treatment process. Additionally, preservatives, flavor enhancers, and colorants used in certain jam varieties may introduce chemical pollutants that require specialized treatment.
Cleaning Agents
Equipment cleaning, an essential aspect of food production, involves the use of detergents and sanitizers. These cleaning agents can introduce chemicals that alter the pH levels of wastewater and contribute to contamination. The presence of caustic cleaning solutions can also pose challenges for biological treatment systems.
Nutrients
Some additives in jam production contribute to elevated nitrogen and phosphorus levels in the wastewater, which can lead to nutrient pollution. If not properly managed, this can result in eutrophication in water bodies, leading to algal blooms that threaten aquatic life.
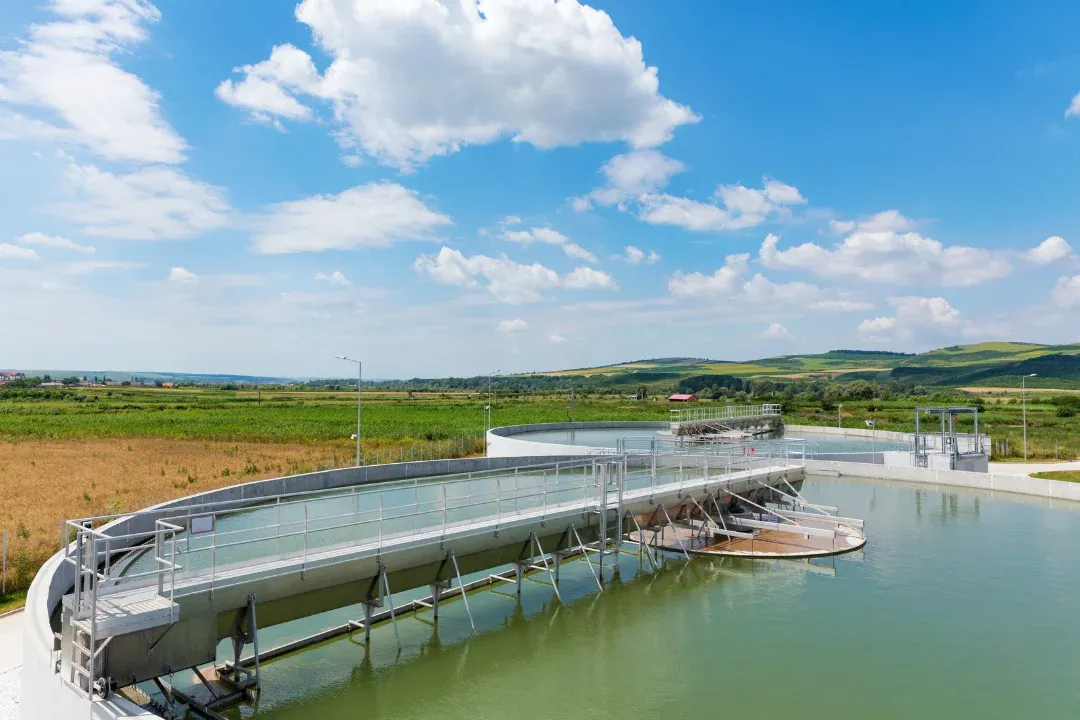
Sustainable Wastewater Treatment Solutions
To reduce the environmental impact of wastewater from jam and jelly production, manufacturers can adopt sustainable wastewater treatment practices. These methods focus on reducing pollutant loads, conserving water, and optimizing treatment efficiency.
Pre-Treatment: Screening and Filtration
The first step in wastewater treatment is removing large solid particles like fruit pulp, peels, and seeds. This can be done through mechanical screening or filtration systems, which help prevent blockages in downstream treatment processes. Additionally, sedimentation tanks can be used to settle out heavy organic solids, improving the overall efficiency of the treatment process.
By addressing large contaminants early, manufacturers can reduce the strain on biological or chemical treatment systems later in the process. Effective pre-treatment is essential for managing high concentrations of organic matter typical in jam production.
Anaerobic Digestion for Organic Matter
One of the most effective ways to handle high levels of organic matter and sugars in jam and jelly wastewater is through anaerobic digestion. This process involves breaking down organic materials in the absence of oxygen, converting them into biogas, which can be captured and used as an energy source within the production facility. This not only reduces the BOD and COD of wastewater but also promotes energy recovery from waste, improving the overall sustainability of the plant.
Anaerobic digestion systems are ideal for treating wastewater with high organic loads, such as that from fruit processing. They also produce digestate, a nutrient-rich byproduct that can be used as fertilizer, further contributing to circular economy practices.
Biological Treatment for Reducing BOD and COD
After pre-treatment, the wastewater typically undergoes biological treatment, which is one of the most common and effective methods for reducing organic load in food production wastewater.
Aerobic Treatment Systems: These systems introduce oxygen into the wastewater, encouraging the growth of aerobic bacteria that consume organic matter. Activated sludge systems or trickling filters are commonly used in this phase. They are effective in significantly reducing BOD and COD levels, ensuring the wastewater is suitable for discharge or further treatment.
Sequencing Batch Reactors (SBRs): An SBR system can treat wastewater in batch mode, offering flexibility and control over treatment processes. It is highly effective for removing organic material and nutrients, ensuring regulatory compliance with effluent standards.
Membrane Filtration Technologies
To further enhance water recovery and improve treatment quality, membrane filtration technologies such as Ultrafiltration (UF) and Reverse Osmosis (RO) can be used. These processes effectively remove dissolved solids, sugars, and even microorganisms from the wastewater. RO systems are especially useful in reducing salinity and achieving high-quality water, which can be reused within the facility for non-potable purposes like cleaning or irrigation.
Membrane Bioreactors (MBRs), a combination of biological treatment and membrane filtration, are also gaining popularity for treating wastewater in the food industry. MBRs offer high removal rates of organic matter and suspended solids, making the treated water suitable for reuse or safe discharge.
Nutrient Removal and Recovery
Wastewater from jam and jelly production may contain elevated levels of nitrogen and phosphorus, which can cause nutrient pollution if not adequately treated. Biological nutrient removal (BNR) processes, such as nitrification-denitrification and phosphorus removal, are commonly employed to address this issue.
In addition to removal, some manufacturers are exploring nutrient recovery technologies to capture and reuse nitrogen and phosphorus from wastewater. These nutrients can be transformed into fertilizers, providing an additional revenue stream and supporting agricultural sustainability.
Zero-Liquid Discharge (ZLD) Systems
In regions where water scarcity is a concern, some manufacturers are adopting Zero-Liquid Discharge (ZLD) systems. These systems are designed to recover nearly all the water from wastewater, leaving behind solid waste that can be further processed or safely disposed of. ZLD technology is a comprehensive solution for minimizing water use and eliminating liquid effluent discharge, making it ideal for companies looking to achieve the highest standards of environmental stewardship.
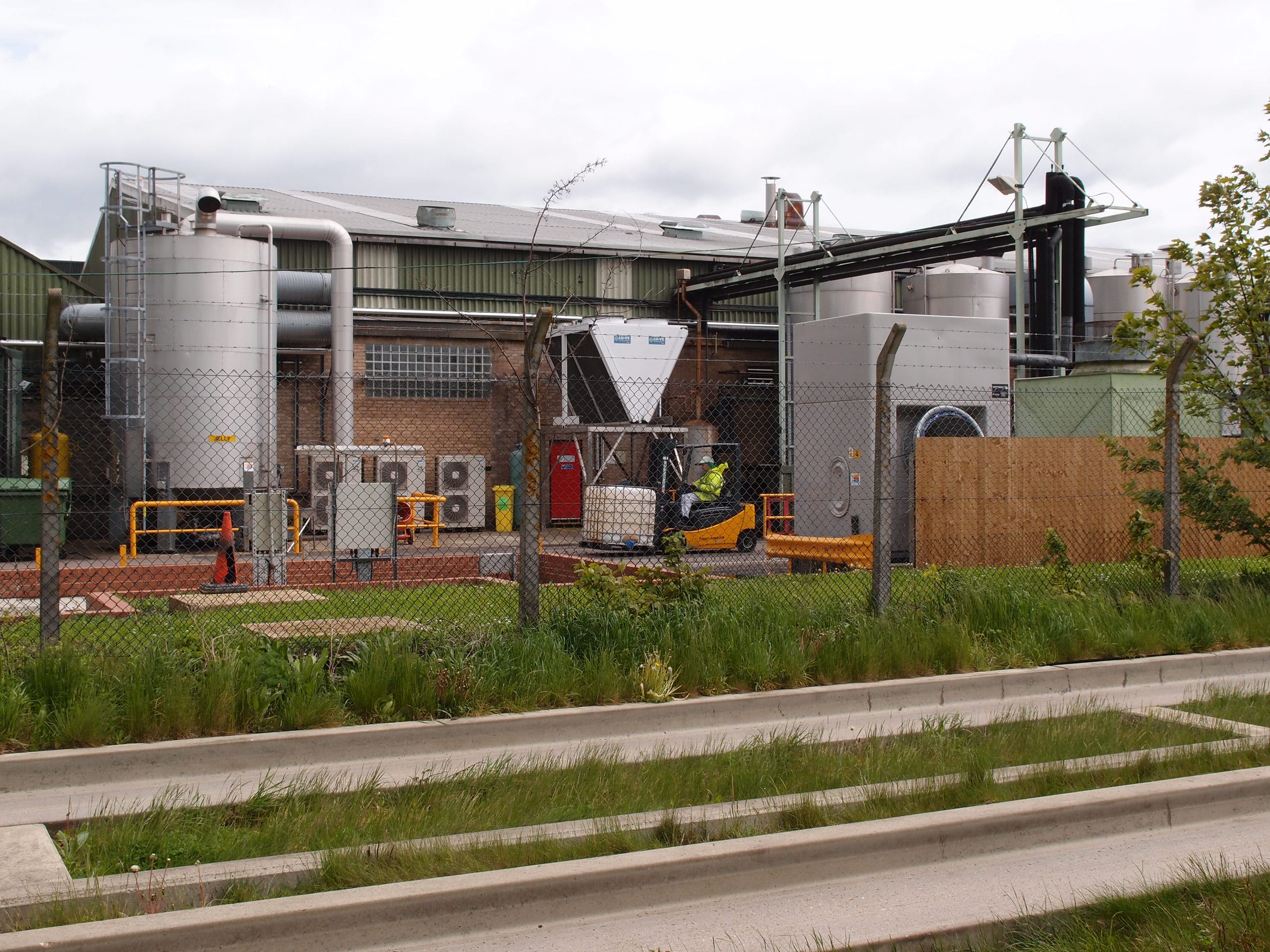
Water Reuse Strategies
One of the most effective ways to reduce the water footprint of jam and jelly production is through water reuse. By recycling treated wastewater within the plant, manufacturers can significantly reduce their freshwater consumption. Recycled water can be used for cleaning equipment, cooling processes, or even in non-potable production applications.
Implementing water-efficient equipment, such as low-flow cleaning systems and water recovery devices, can further reduce water use. Manufacturers are also exploring rainwater harvesting and other renewable water sources to supplement their water needs and decrease reliance on municipal supplies.
Monitoring and Automation
To optimize wastewater treatment processes and ensure compliance with environmental regulations, it is crucial to implement real-time monitoring systems. These systems continuously measure key parameters such as BOD, COD, pH, and nutrient levels, allowing operators to adjust treatment processes as needed.
Automation plays a key role in modern wastewater treatment, enabling precise control over treatment stages and reducing human error. Automated systems can also help manufacturers optimize energy use, chemical dosing, and water reuse, contributing to overall process efficiency and sustainability.
Conclusion
The jam and jelly processing industry faces unique challenges in managing wastewater due to the high levels of organic matter, sugars, and nutrients present in effluents. However, by adopting sustainable wastewater treatment practices, manufacturers can not only reduce their environmental impact but also improve operational efficiency and resource conservation.
Implementing technologies like anaerobic digestion, membrane filtration, and biological nutrient removal can effectively treat wastewater and even provide opportunities for resource recovery. Additionally, water reuse and real-time monitoring systems can further enhance sustainability efforts in jam and jelly production facilities.
As consumer demand for environmentally responsible food products continues to grow, the jam and jelly industry must remain committed to innovative and sustainable wastewater management solutions. By investing in these practices, manufacturers can safeguard the environment while also securing a competitive edge in the market.