In the vibrant landscape of textile production, the allure of color, texture, and innovation often overshadows a pressing concern: wastewater management. The textile industry stands as one of the most significant contributors to industrial wastewater, characterized by a complex cocktail of dyes, chemicals, and contaminants. However, amidst this challenge lies a beacon of hope – advanced wastewater treatment technologies. Let's explore the journey of textile industry wastewater treatment and the transformative impact it holds for sustainability.
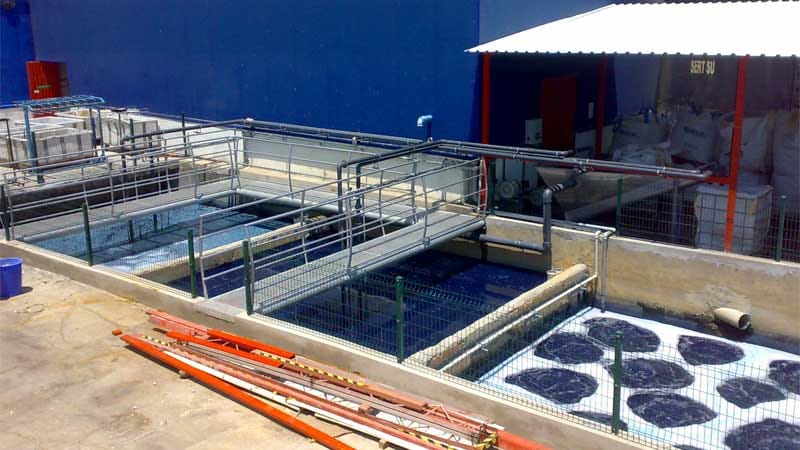
A Journey of Innovation
The textile industry has embarked on an extraordinary journey of innovation in wastewater treatment, compelled by the urgent need to confront the environmental challenges posed by textile effluents. Initially, traditional treatment methods such as sedimentation and chemical coagulation formed the cornerstone of wastewater management, paving the way for subsequent advancements. However, acknowledging the limitations of these conventional approaches, the textile wastewater treatment landscape has undergone significant evolution.
In the present day, modern textile wastewater treatment plants seamlessly integrate a wide array of state-of-the-art technologies and methodologies. These facilities employ a blend of physical, chemical, and biological processes to efficiently eliminate pollutants and purify water. Through relentless research and development efforts, the industry has engineered sophisticated treatment systems capable of effectively addressing the intricate composition of textile effluents.
This journey of innovation underscores the industry's unwavering commitment to environmental sustainability and conscientious stewardship. By embracing emerging technologies and refining treatment processes, textile manufacturers endeavor to minimize their environmental footprint and mitigate the adverse impact of their operations on water resources and ecosystems. Consequently, textile wastewater treatment has emerged as a pivotal aspect of the industry's endeavors to cultivate a more sustainable future.
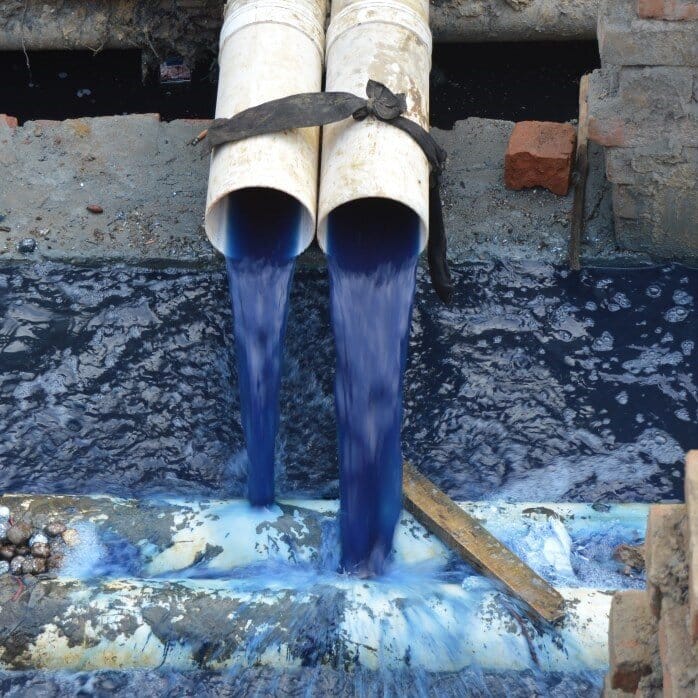
The Intricacies of Textile Wastewater Treatment
Textile wastewater treatment plants operate as multifaceted systems, meticulously designed to address the diverse composition of textile effluents. These facilities are structured with a series of stages and components, each serving a specific function in the purification process.
Preliminary Screening:
At the onset of treatment, wastewater undergoes preliminary screening to remove large solids and debris. This step is crucial for protecting downstream equipment from potential damage or clogging. Screening devices such as bar screens or rotary drum screens effectively capture bulky materials, preventing interference with subsequent treatment processes.
Primary Treatment:
Following preliminary screening, the wastewater progresses to the primary treatment stage. Here, physical and chemical processes are employed to further separate suspended solids and reduce the organic load of the effluent. Primary treatment commonly involves processes such as sedimentation, flotation, and chemical coagulation. During sedimentation, gravity causes suspended particles to settle to the bottom of tanks, forming a sludge layer, while flotation utilizes air bubbles to lift suspended solids to the surface for removal. Chemical coagulants, such as alum or ferric chloride, aid in the aggregation of fine particles, facilitating their precipitation and subsequent removal.
Biological Treatment:
After primary treatment, the wastewater enters the biological treatment phase, where microorganisms play a pivotal role in degrading organic pollutants. Biological treatment can occur through aerobic or anaerobic processes, depending on the availability of oxygen. In aerobic treatment, microorganisms utilize oxygen to metabolize organic matter, while anaerobic treatment occurs in the absence of oxygen, with microorganisms decomposing organic compounds through fermentation. Common biological treatment systems include activated sludge processes, sequencing batch reactors (SBRs), and anaerobic digesters. These systems foster the growth of diverse microbial communities, which efficiently break down organic contaminants, thereby reducing the biochemical oxygen demand (BOD) and chemical oxygen demand (COD) of the effluent.
Secondary Clarification and Disinfection:
Following biological treatment, the wastewater undergoes secondary clarification to remove any remaining suspended solids and microbial biomass. Clarifiers or sedimentation tanks allow settled solids to be separated from the clarified water, which is then subjected to disinfection. Disinfection processes, such as chlorination, ultraviolet (UV) irradiation, or ozonation, target pathogens and microbial contaminants, ensuring the safety of the treated effluent prior to discharge or reuse.
In essence, textile wastewater treatment plants are intricate systems that employ a combination of physical, chemical, and biological processes to purify wastewater and safeguard the environment. Through meticulous design and operation, these facilities uphold stringent regulatory standards and contribute to sustainable water management practices within the textile industry.
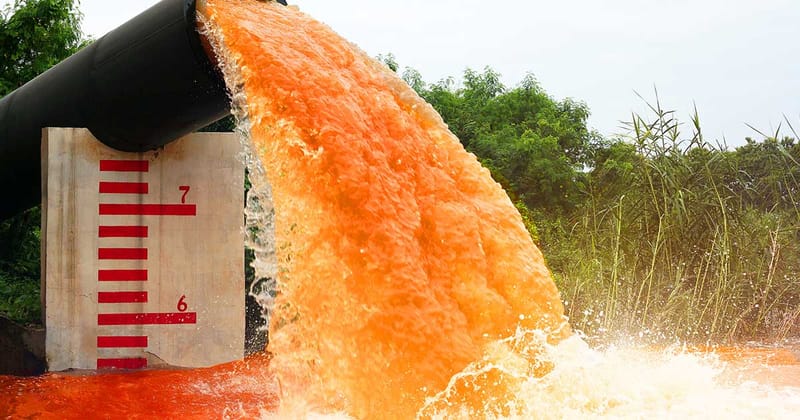
Embracing Sustainability: A Vision for the Future of the Textile Industry
In recent years, the textile industry has been focusing more on being eco-friendly, which means being kind to the environment. This change has led to new ways of treating wastewater, the dirty water that comes from making textiles, as companies try to pollute less and stay competitive. Nowadays, modern textile wastewater treatment plants use methods that are good for the environment, like reusing water, getting back valuable stuff from the dirty water, and using less energy.
Water Recycling and Getting Back Resources:
A big part of being eco-friendly in treating wastewater from textiles is reusing water. By cleaning up the dirty water and using it again in making textiles, companies can use less fresh water and be kinder to the planet. Also, they're finding ways to get back useful things from the dirty water, like colors, chemicals, and fibers, which they can use again, making their production process more sustainable.
Using Less Energy:
As well as reusing water and getting back useful stuff, using less energy is also important for treating wastewater in a sustainable way. Textile companies are starting to use technologies and methods that use less energy, like making gas from waste and using renewable energy sources, to reduce their energy use and make less pollution. This helps them save money and be kinder to the environment.
Working Together and Being Creative
Making textile wastewater treatment better for the environment is a team effort. Everyone involved – companies, tech providers, governments, and communities – needs to work together to come up with solutions that help the planet. They're also always trying out new ideas and ways of doing things to make treating wastewater from textiles even better for the environment.
Following the Rules
There are rules and laws that tell companies how to treat wastewater from textiles to protect the environment and keep people healthy. Governments are making these rules stricter to make sure companies are being responsible. By following these rules and finding ways to help the environment, textile companies can show that they care about the planet and follow good business practices.
Looking to the Future
We're not done yet! There's still a lot to do to make treating wastewater from textiles even better for the environment. We need to keep coming up with new ideas, working together, and following the rules to keep making progress. By using technology, being creative, and working together, we can create a textile industry that's kinder to the planet and keeps our water and environment clean for future generations. Making textile wastewater treatment better isn't just about following rules – it's about changing how we do things to make our planet healthier and happier.